The role of coolant in the machining of aerospace parts is evolving. The practice of the shop for many years has been to spray the coolant directly into the processing area. However, high-pressure cooling technology now has the advantage of accurately directing the coolant to the actual cutting zone. Excitingly, this new technology has been widely used with the increase of coolant capacity and the introduction of new tool concepts for many modern CNC machine tools. What makes a difference If you want to make the coolant work effectively and produce a different effect in modern processing, you need to configure high-pressure jet cooling, the flow must be large enough, and the spray direction should be correct. A stream of the same coolant or the passage of coolant through the processing area is no longer sufficient. In addition, the rational use of high pressure cooling (HPC) can have significant effects in terms of chip formation, heat distribution, adhesion of workpiece materials on the cutting edge, surface integrity and tool wear. Through the basic processing factors such as increasing production efficiency and processing quality, the competitiveness is correspondingly improved. High pressure cooling (HPC) applications have been very different in the conventional processing of stainless steel and low carbon steel, but this technique performs even better in the processing of difficult-to-machine materials such as titanium alloys and heat-resistant superalloys. Recent extensive research and development on high pressure cooling (HPC) has made it easier to use and more attractive. The Jetbreak system pioneered the concept of high pressure cooling. In the 1880s and 1990s, Sandvik Coromant developed the first generation of high pressure cooling system Jetbreak. Studies have shown that ultra-high pressure, direction-accurate coolant jets of up to 100 – 1000 bar have become part of the cutting tool for demanding materials with machinability and chip control. The coolant jet forms a hydraulic wedge between the chip and the cutting edge, and as the temperature of the processing zone decreases, the contact length of the chip and the cutting edge is shortened. Another interesting effect is that the coolant jet affects the chipping of the chips, which improves chip control and, in some cases, chip breaking. With the use of non-standard tools, the Jetbreak system has become an ideal solution for materials with poor processability or chip breaking. The distribution of coolant pressure and the size of the nozzle can have a large effect on the processing results. By adjusting the jet parameters, different chipping effects can be obtained, and it is possible to guide the strips to the desired direction, even to improve the length of the chips. The practical application of the Jetbreak system is limited, mainly to solve problems encountered in the petroleum, aerospace and rolling bearing industries. The Jetbreak system requires a special non-standard tool holder, and the technology is mainly applied to vertical lathes. High-pressure cooling technology becomes the industry standard Many modern CNC machine tools come standard or optional with a pressure system of 70 to 100 bar, which is sufficient for high-pressure cooling technology and in conventional machining centers, turning centers, vertical machines and many more Task machine tool processing for excellent machining results. Standard equipment is sufficient to provide a coolant passage to the jet application area. When using high-pressure cooling for machining, the use of modular tools is the best method. It not only ensures a minimum stop loss by a quick tool change, but also provides a reliable and efficient way to direct coolant from the machine to the cutting edge. aisle. Coromant Capto? The modular quick-change tooling system is the basis for the development of Jetbreak and Sandvik Coromant's new modular high-pressure cooling tool CoroTurn HP. Coromant Capto has become an ISO standard and is widely used by many CNC machine tools. CoroTurn HP for turning high pressure cooling produces parallel and precise coolant injection, creating a hydraulic wedge between the insert and the chip, affecting chip formation and flow and reducing the temperature in the cutting area. The nozzle mounted near the cutting edge accurately ejects a high velocity coolant jet, forcing the chips away from the blade surface and allowing the chips to cool and break, allowing the chips to facilitate chip evacuation. Standard nozzle sizes range from 1 mm to 0.6 mm to 1.2 mm for specific optimized applications. 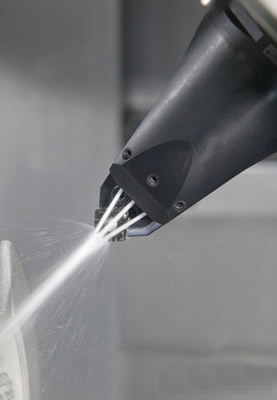
CoroTurn HP produces parallel, precise coolant injection Even with coolant pressures as low as 10 bar, high pressure cooling technology can be used to achieve significant benefits when finishing steel, stainless steel, aluminum alloys, titanium alloys and superalloys. In addition to the higher process safety resulting from better chip control, high pressure cooling significantly extends tool life (up to 50%); the potential for higher cutting speeds results in significant savings in production costs of. Cutting speed has a greater impact on cutting temperature and tool wear than any other factor. If the machining of the titanium alloy is beyond the reasonable processing area, the faster cutting speed will lead to a sharp shortening of the tool life, but in a similar way to increase the feed rate, the tool life is shortened less obvious. Therefore, it is a more attractive solution to change the feed rate to improve the metal removal rate. However, the use of high feed rates is not always a perfect strategy. The increase in feed rate will certainly produce greater cutting force, but it will also affect chip control. With higher cutting speeds without the usual temperature rise and reduced tool life, high pressure cooling technology has the potential to improve processability. No need to use higher feed rates for higher cutting forces, and significant cooling effects can be produced. For ISO class S materials, the cutting length can be kept the same when the cutting speed is increased by 20%. Internal turning is also an area where high pressure cooling technology can play an important role in helping to ensure good chip formation and improving the shear properties of materials when machining difficult materials such as titanium. In this way, higher machining safety and longer tool life are achieved during the boring process. When using a mast to machine relatively large and deep holes, such as landing gear parts, it is advantageous to use modular cutters with modular interfaces on the front and rear ends. The ability to quickly and accurately replace the smaller cutting modules clamped on the front end of the mast on the machine provides considerable flexibility for various cuts in a single setup. CoroTurn SL combines a cutting head with a serrated interface with a damping boring bar for boring large holes with a 10x depth of the mast and high pressure cooling.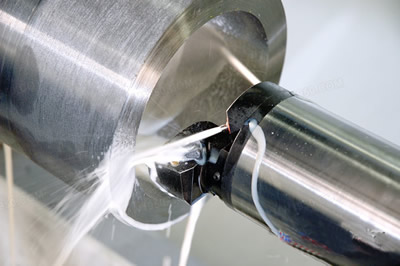
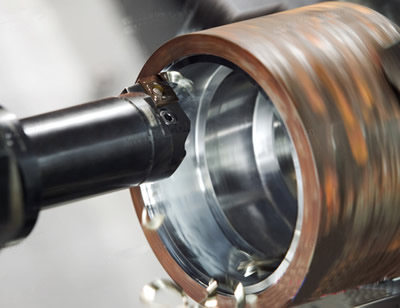
CoroTurn SL combines a cutting head with a serrated interface with a damping boring bar for boring large holes with a diameter of 10 times the diameter of the mast. It also has the capability of high pressure cooling for high pressure cooling of milling by high pressure cooling. Technology also brings benefits to milling. The CoroMill 690 is a long-edge end mill with high pressure cooling for titanium machining. Its radial cutting edge consists of a number of blades, and each blade has a corresponding coolant nozzle to provide high pressure injection. Instead of using the entire axial depth of the milling cutter, a plug can be used instead of the nozzle, which avoids unnecessary air injection and loses cooling pressure. The nozzle at the end of the tool helps to remove chips and avoid the chip's re-cutting effect (especially in cavity machining). In order to ensure the correct value of the coolant flow and pressure, a dedicated calculator can be used to achieve the best application of high pressure cooling on the milling cutter (input machine coolant flow rate and pressure, cutting parameters, axial depth of cut and tool parameters, etc.) ). The calculator will calculate the optimum nozzle size to reduce flow requirements while maintaining the selected orifice to maintain high pressure flow as the coolant passes. The active chemistry of titanium alloys makes it easy to bond to the cutting edge during processing. This phenomenon usually causes chip re-cutting effects and chipping, which affects the life of the tool. High pressure cooling is a common method of preventing workpiece material from sticking to the cutting edge when processing titanium alloys and other viscous materials.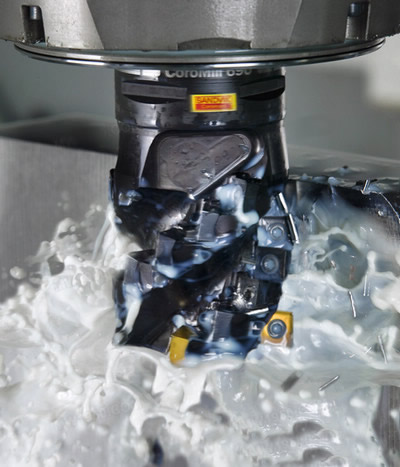
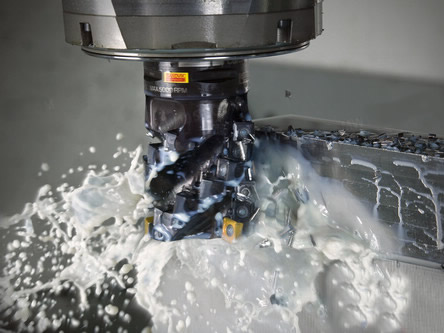
CoroMill 690 is an optimized high-pressure cooling process for high-altitude cooling of long-edge end mills for titanium machining. It should not be considered as a remedy for other application factors (eg, unsuitable blades, instability and incorrectness) The cutting parameters, etc.) are the means of causing the disadvantages. This technique is an "optimizer" when the process settings are basically correct. This concept provides solutions for shorter machining times, improved part quality consistency and higher process safety in turning and milling. The need for optimization of various machining processes, especially when machining of chip formation and difficult-to-machine materials is dominant, high-pressure cooling technology that is already widely available on the machine window is undoubtedly an attractive option. The increasing popularity of multi-tasking machines and the new generation of vertical lathes has highlighted the benefits of high-pressure cooling, especially from the perspective of chip control. As manufacturers increasingly use these machines to machine aerospace parts made of difficult-to-machine materials, it becomes increasingly important to eliminate the hassle caused by the accumulation of chips.
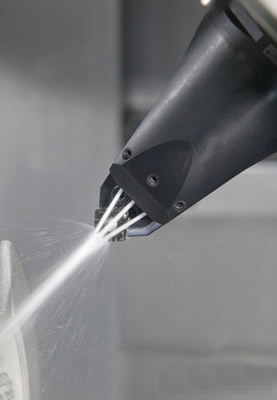
CoroTurn HP produces parallel, precise coolant injection Even with coolant pressures as low as 10 bar, high pressure cooling technology can be used to achieve significant benefits when finishing steel, stainless steel, aluminum alloys, titanium alloys and superalloys. In addition to the higher process safety resulting from better chip control, high pressure cooling significantly extends tool life (up to 50%); the potential for higher cutting speeds results in significant savings in production costs of. Cutting speed has a greater impact on cutting temperature and tool wear than any other factor. If the machining of the titanium alloy is beyond the reasonable processing area, the faster cutting speed will lead to a sharp shortening of the tool life, but in a similar way to increase the feed rate, the tool life is shortened less obvious. Therefore, it is a more attractive solution to change the feed rate to improve the metal removal rate. However, the use of high feed rates is not always a perfect strategy. The increase in feed rate will certainly produce greater cutting force, but it will also affect chip control. With higher cutting speeds without the usual temperature rise and reduced tool life, high pressure cooling technology has the potential to improve processability. No need to use higher feed rates for higher cutting forces, and significant cooling effects can be produced. For ISO class S materials, the cutting length can be kept the same when the cutting speed is increased by 20%. Internal turning is also an area where high pressure cooling technology can play an important role in helping to ensure good chip formation and improving the shear properties of materials when machining difficult materials such as titanium. In this way, higher machining safety and longer tool life are achieved during the boring process. When using a mast to machine relatively large and deep holes, such as landing gear parts, it is advantageous to use modular cutters with modular interfaces on the front and rear ends. The ability to quickly and accurately replace the smaller cutting modules clamped on the front end of the mast on the machine provides considerable flexibility for various cuts in a single setup. CoroTurn SL combines a cutting head with a serrated interface with a damping boring bar for boring large holes with a 10x depth of the mast and high pressure cooling.
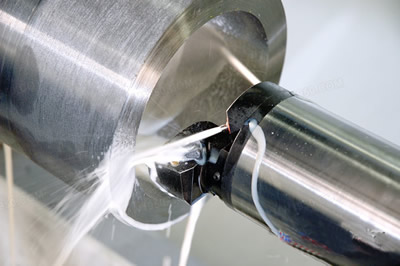
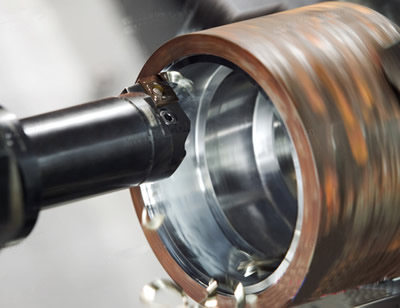
CoroTurn SL combines a cutting head with a serrated interface with a damping boring bar for boring large holes with a diameter of 10 times the diameter of the mast. It also has the capability of high pressure cooling for high pressure cooling of milling by high pressure cooling. Technology also brings benefits to milling. The CoroMill 690 is a long-edge end mill with high pressure cooling for titanium machining. Its radial cutting edge consists of a number of blades, and each blade has a corresponding coolant nozzle to provide high pressure injection. Instead of using the entire axial depth of the milling cutter, a plug can be used instead of the nozzle, which avoids unnecessary air injection and loses cooling pressure. The nozzle at the end of the tool helps to remove chips and avoid the chip's re-cutting effect (especially in cavity machining). In order to ensure the correct value of the coolant flow and pressure, a dedicated calculator can be used to achieve the best application of high pressure cooling on the milling cutter (input machine coolant flow rate and pressure, cutting parameters, axial depth of cut and tool parameters, etc.) ). The calculator will calculate the optimum nozzle size to reduce flow requirements while maintaining the selected orifice to maintain high pressure flow as the coolant passes. The active chemistry of titanium alloys makes it easy to bond to the cutting edge during processing. This phenomenon usually causes chip re-cutting effects and chipping, which affects the life of the tool. High pressure cooling is a common method of preventing workpiece material from sticking to the cutting edge when processing titanium alloys and other viscous materials.
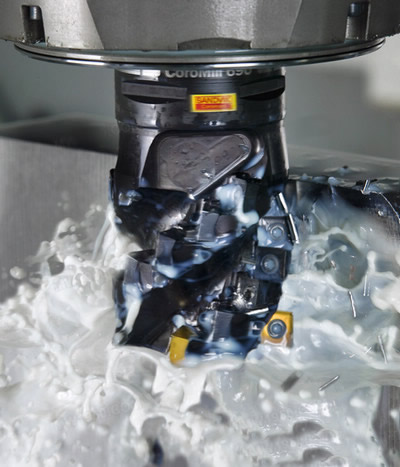
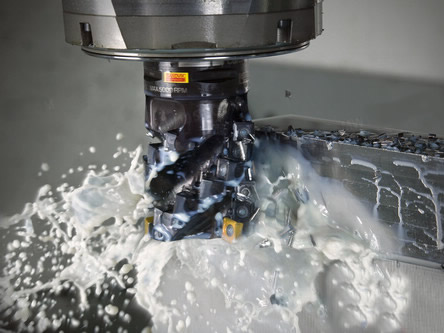
CoroMill 690 is an optimized high-pressure cooling process for high-altitude cooling of long-edge end mills for titanium machining. It should not be considered as a remedy for other application factors (eg, unsuitable blades, instability and incorrectness) The cutting parameters, etc.) are the means of causing the disadvantages. This technique is an "optimizer" when the process settings are basically correct. This concept provides solutions for shorter machining times, improved part quality consistency and higher process safety in turning and milling. The need for optimization of various machining processes, especially when machining of chip formation and difficult-to-machine materials is dominant, high-pressure cooling technology that is already widely available on the machine window is undoubtedly an attractive option. The increasing popularity of multi-tasking machines and the new generation of vertical lathes has highlighted the benefits of high-pressure cooling, especially from the perspective of chip control. As manufacturers increasingly use these machines to machine aerospace parts made of difficult-to-machine materials, it becomes increasingly important to eliminate the hassle caused by the accumulation of chips.
Jiangmen Faer Sanitary Co.,Ltd , https://www.faersanitarys.com