The use of axial ultrasonic vibration drilling technology to machine micro-holes (0.5mm or less) can extend the life of the drill bit, improve the accuracy of the hole and the surface quality of the hole wall, and reduce the burr of the drilling exit, which has excellent process effect. This paper introduces a design method of the ultrasonic vibration drilling machine spindle. With this design scheme, the original spindle of the drilling machine can be replaced by the ultrasonic vibration spindle without changing the other structure of the drilling machine. The modification of the machine tool can be completed, and the structure is compact and convenient to use.
![]() 1. Keyway 2. Drive shaft 3. Rear matching block 4, 6. Piezoelectric ceramic 5. Electrode 7. Front matching block 8. Luff 9. Current collecting ring 10. Elastic claw 11. Round sleeve Spindle structure diagram |
1 Spindle structure design
The drill chuck is installed at the lower end of the ordinary drilling machine spindle, and the rotary motion and the axial feed motion should be completed. In addition to the above movement, the ultrasonic vibration drill spindle should also have the function of axial ultrasonic vibration.
The vibrator in the ultrasonic vibration main shaft can be a sandwich type piezoelectric ceramic transducer (CDE segment in the figure), and its electroacoustic conversion efficiency can reach about 90%, and the structure is very compact. It consists of a pair of piezoceramic plates, electrodes and front and rear matching blocks. Since the ultrasonic transducer used for micro hole processing has less power and relatively less heat, there is no special cooling system.
The front matching block and the horn can be made in one piece. The ordinary drill chuck has a complicated structure and a large mass, and is easy to damage the resonance state of the spindle system, resulting in a large reduction in the bit amplitude. Therefore, a simple elastic collet is designed at the end of the horn, and the elastic collet has four elastic claws for clamping the drill bit. A current collecting ring is mounted on the small end of the horn for transmitting the current required for the transducer to operate.
The rear matching block is integrated with the stepped drive shaft, and the small end of the drive shaft is provided with a keyway for sliding cooperation with the drill bed pulley to drive the spindle system to rotate. A small radial end bearing and a small end of the transmission shaft are respectively provided with a radial ball bearing for supporting the mounting main shaft, and the outer ring of the bearing is matched with the spindle sleeve of the drilling machine, and the sleeve with the tooth groove can drive the main shaft for axial direction. Feed.
2 transducer and horn design principle
The voltage of the ultrasonic frequency is applied to the two poles of the piezoelectric ceramic, and the thickness thereof changes with the voltage, so that longitudinal ultrasonic vibration is generated, and the longitudinal vibration wave propagates in the forward and backward directions. When the medium of the propagating wave changes, the refraction and reflection of the wave will occur at the interface, and the ratio of the amount of reflection depends on the density ratio of the two media. The greater the density ratio, the greater the amount of reflection. Since the density ratio of steel to air is very large, it can be considered that the waves propagating to both ends of the main shaft are reflected back. The reflected wave is half a cycle later than the incident wave. It is superimposed on the wave directly emitted from the piezoelectric ceramic. The amplitude increases in some sections, and the amplitude decreases on some sections. The amplitude is always zero, forming a standing wave conduction. If the system consisting of a transducer, a horn, etc. happens to be an integer multiple of the 1/2 wavelength of the sound wave, the system is in a resonant state, and the resonance condition can be expressed as
If the structural damping and surface acoustic wave radiation of the medium are not considered, the amplitude and frequency of the acoustic wave do not change when propagating in an equal-section elastic medium. The variable cross-section rod is different in the resonant state. When the vibration wave is transmitted from the end with the larger cross-section to the end with the smaller cross-section, the amplitude will increase, so the variable-section rod has resonance or close to the resonance state. Variable amplitude function. For the step horn, the following relationship exists between the output amplitude A 2 and the input amplitude A 1
In order not to damage the resonance state of the spindle system, the bearing for the fixed spindle should be placed at the node (that is, the stagnation point where the amplitude is always equal to zero), and the drill bit should be installed at the antinode (the maximum amplitude) so that the drill bit can be obtained. Large amplitude.
3 Determination of the size of the spindle structure
The lateral dimension of the main shaft is mainly limited by the size of the inner hole of the drill sleeve. In order to obtain a large vibration power and vibration amplitude, the inner hole space of the sleeve should be utilized as much as possible, and the piezoelectric ceramic piece with a larger diameter should be selected. The diameter of the front and rear matching blocks of the transducer can be the same as the diameter of the piezoelectric ceramic piece. For the convenience of connecting the wires, the electrode diameter can be 8 to 10 mm larger than the diameter of the piezoelectric ceramic piece. When the spindle system is in resonance, the amplitude obtained at the drill bit is the largest. At this time, the total length of the main shaft should be an integral multiple of half wavelength. The length of each part of the main shaft should also be determined according to the respective wavelengths.
The drive shaft (AC section in the figure) and the horn (EG section) are elastic rods made of the same material, and the wavelength can be calculated by the following formula.
There are elastic materials such as steel in the transducer, and non-elastic materials such as piezoelectric ceramics. The length of each part of the transducer (CE segment in the figure) is more complicated and can be performed in three steps. (1) According to the inner hole space of the spindle sleeve and the product catalog of the piezoelectric ceramic manufacturer, the size of the piezoelectric ceramic piece (including the thickness l 0 ) is selected; (2) the thickness of the electrode is determined to be l 3 , and the electrode generally adopts a conductive property. Good aluminum or copper sheet, in order to meet the needs of connecting wires, the thickness can be 3 ~ 5mm; (3) determine the length of the front and rear matching blocks l 2 and l 1 , for the design is convenient, the length of the front and rear matching block is desirable The same value, ie l 1 = l 2 , the length of the matching block l 1 can be calculated as follows
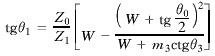
l 0 is the thickness of the piezoelectric ceramic piece; l 1 is the length of the rear matching block; l 2 is the length of the front matching block; l 3 is the thickness of the electrode; C 0 is the longitudinal wave velocity of the piezoelectric ceramic; C 1 is the longitudinal wave velocity of the matching block; C 3 Is the longitudinal wave velocity of the electrode; r 0 is the piezoelectric ceramic density; r 1 is the matching block density; r 3 is the electrode density; k 33 is the piezoelectric ceramic electromechanical coupling coefficient; w 1 is the resonant circular frequency; S 0 , S 1 , S 3 is the cross-sectional area of ​​the piezoelectric ceramic piece, the rear matching block and the electrode; q 0 , q 1 , q 3 , Z 0 , Z 1 , Z 3 , m 3 , W are all intermediate parameters.
When the matching block length l 1 is calculated by using the above formula, the specific value of each physical parameter must be determined first. The resonant circle frequency w 1 is the product of the selected ultrasonic generator operating frequency f and 2Ï€; the piezoelectric ceramic sheet thickness l 0 , the density r 0 , the electromechanical coupling coefficient k 33 , etc. can be obtained from the manufacturer's product description; The front and rear matching blocks and the horn and the transmission shaft can be made of high-quality carbon structural steel or titanium alloy steel. The density r 1 , the longitudinal wave velocity C 1 , the density of the electrode r 3 and the longitudinal wave velocity C 3 can be obtained from the relevant material manual. Find.
Using the above design scheme, the Z403 bench drilling machine has been modified to obtain satisfactory results. The ultrasonic vibration amplitude on the drill bit is more than 2μm.
Advanced waterproof treatment process, the product has good water proof, not easy to break when used.
·Excellent scientific and environmentally friendly formula combination resin makes good flexibility, water resistance and wear resistance, high grinding efficiency, good surface finish and good consistency product.
· Sharp good-life,general purpose ,longer life time..
Craft Paper Abrasive Paper,Wet Abrasive Paper,special latex paper,Emery Cloth Sanding Belts
ZHENJIANG DINGHUI ABRASIVE TOOLS CO.,LTD , https://www.dhabrasivepaper.com