product description
The synchronous tooth holder on the synchronizer produced by our company has three holes and different apertures. The process requirement for drilling is to ensure that the distance between the center of the three holes and the plane B is H±0.15mm, the symmetry to the reference D is 0.15mm, the aperture φd+0.3 +0 and the hole depth L+0.3 +0, the structure is as follows Figure 1 shows.

figure 1
Synchronous toothed universal die design
The three-division hole of the synchronous tooth drill has the problem that the end face size cannot be guaranteed and the personal operation is difficult. There are more than 20 varieties of synchronous gears produced by our company, and there are eight pairs of drills. Each time a product is processed, the mandrel, drill sleeve and gasket are replaced. The gasket is easy to store the chips during the processing, resulting in the hole and the end face being out of size. Due to the poor versatility of the fixture, the fixture management is disordered and the auxiliary time is increased. Since the different synchronous teeth have different outer diameters, the distance from the center of the drill to the B surface shown in FIG. 1 is different, the centering dimensions are different, and the diameters of the holes are different.
List the data by reviewing the drawings and statistics. First of all, for the problem of different outer diameters of different products (φ157.4mm, φ176.2mm and φ192mm), the drill template is designed into three specifications when designing the drill to meet the three outer diameter dimensions of the product (see Figure 2). In order to adapt to the change of its outer diameter; secondly, for different products, the distance from the center of the hole to be drilled to the B surface shown in Figure 1 is different, the replacement of the positioning mandrel is solved; third, for the hole to be drilled, the aperture Different problems, replace the drill sleeve to solve. After the above considerations, a universal drilling mold with a synchronous tooth holder is designed, and the fixture structure is shown in FIG.
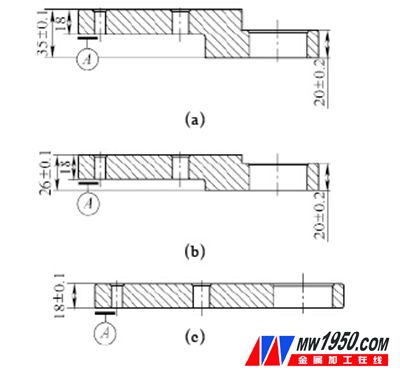
figure 2
How general-purpose drills work
As shown in Fig. 3, the positioning of the product is determined by the end face of the positioning mandrel 14 and the end face and the inner hole of the product of the journal size, and the drill sleeve 15 is cut into the circumferential position of the product groove. When the clamp is used, the product is first mounted on the positioning mandrel 14, and the end surface of the product is closely attached to the end surface of the positioning mandrel. The drill sleeve is inserted into the product slot, and the open platen member 12 is placed, and the shoulder nut 13 is rotated. The first hole can only be machined after the mandrel 5 is tightened. After the first hole is finished, the spherical handle 17 is rotated, the shaft 5 is loosened, and the mandrel is rotated, so that the drill sleeve can be inserted into the product slot to process the second hole. Repeat the above action to machine the third hole. After processing, remove the drill sleeve, loosen the shoulder nut and the pressure plate, and take out the product.
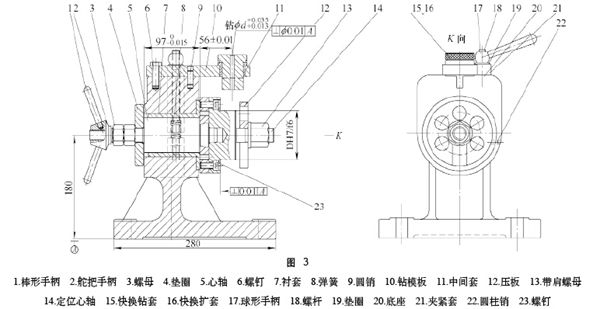
Accuracy analysis of general drilling mold
It can be seen from the structure of the common tooth mold of the synchronous tooth holder that the main factors affecting the processing error of the product are:
1) The fit clearance (δ1) between the product hole and the positioning mandrel affects the depth L of the hole.
2) The distance tolerance (δ2) of the two ends of the positioning mandrel directly affects the distance H3 from the end face of the product to the center of the hole.
3) The fit clearance (δ3) between the flat size of the drill sleeve and the product slot affects the symmetry of the hole to the reference D by 0.15 mm.
4) The clearance (δ4) between the drill sleeve and the drill bit affects the hole size and drilling stability. If the gap is too large, the drill is easy to drill, the drill deflection is larger, and the drilling process is severely vibrating; if the clearance is too small, the drill is prone to occur and the tool wear is caused.
According to the design principle of the fixture, the error is 1/3 to 1/5 of the product tolerance. Therefore, the positioning mandrel size tolerance is f6, δ1 < 1/3 × 0.3 mm. Δ2 takes the sum of the tolerances of the parts of the positioning mandrel ± 0.02 mm. The tolerance of the product slot is ±0.02mm, the flat size of the drill sleeve is f6, and the gap is δ3≤0.10mm. Since the drill sleeve is a standard sizing tool, the inner diameter of the drill sleeve is selected according to the base shaft, and the drill sleeve tolerance is taken as F8 to determine δ4.
Use and precautions
Synchronous toothed universal drilling mold is used to control the axial movement of the mandrel and increase the interchangeability of the mandrel. The design size of the mandrel is 97+0.015 +0.005mm, which must be ensured and the rotation is flexible. After the fixture is assembled, the end face of the base 20 is ensured to have a face size of 97-0 -0.005 mm from the end face of the bushing 7 and a distance of 56 ± 0.01 mm from the end face of the bushing to the center of the drill sleeve. When using, first select the drill template according to the outer diameter of the product: φ157.4mm select picture 2a, φ176.2mm select picture 2b, φ192mm select picture 2c, then select the positioning mandrel according to the inner diameter of the product, and finally according to the slot width of the product Select the drill sleeve for the hole size.
Conclusion
The universal drilling mold of the synchronous tooth holder designed in this paper has strong versatility, meets the process requirements, reduces the cost, and obtains good economic benefits. After the general-purpose drilling mold of the synchronous tooth holder is put into the production site, the sampling rate of the processed product is 100%. It has the characteristics of large versatility, convenient use, simple operation and light weight, and has reference and reference value for other common fixture design.
5050 RGB,2121RGB
Shenzhen Huangtai Photoelectric Co.,Ltd. , https://www.huangtailightstrip.com